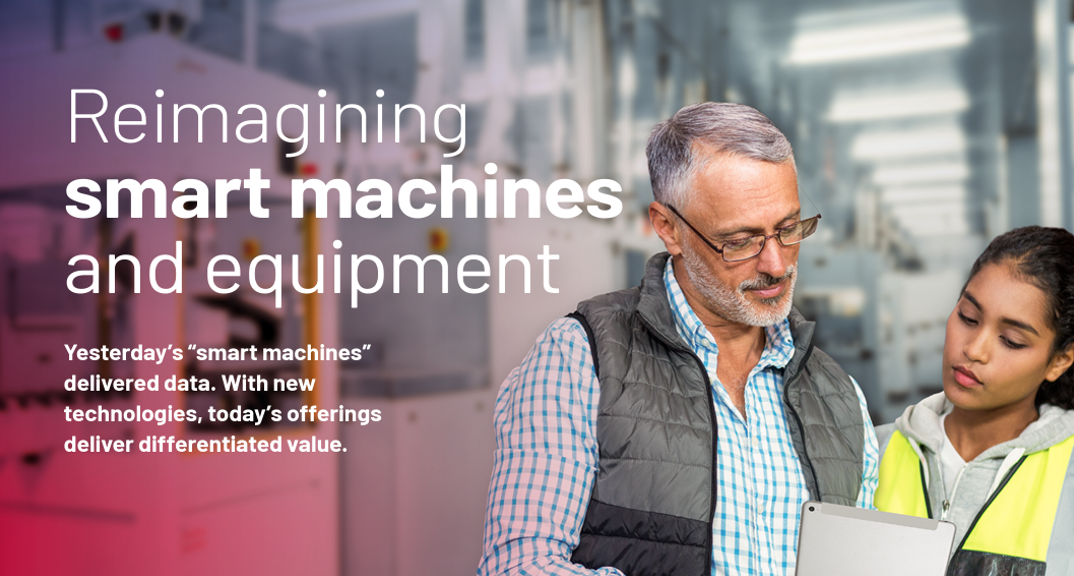
A new world of possibilities is coming into focus. Cycle times. Production rates. Uptime. Not so long-ago measuring asset performance was straightforward.
Those days are gone.
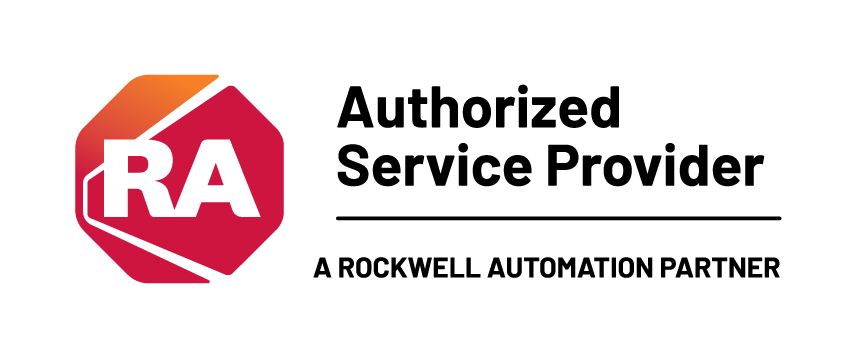
New realities like just-in-time production, multiple SKUs, shorter product lifecycles – and skills shortages – have changed the equation. And ushered in new expectations for machines that are highly productive, and more flexible too. Machines that support easier ways to collaborate and work smarter and equipment built for process efficiency and optimization. Simply put, manufacturers need innovative equipment that meets contemporary challenges.
What matters most
As an OEM, how do you keep up with marketplace challenges? With information-enabled, smart machines and equipment that use advanced technology – and are built on a foundation that securely and safely connects to the production environment and beyond.
Connected digital technologies open new ways to differentiate your equipment – and deliver results that matter most to your customers:
- Better productivity with real-time information
- Faster setup and changeover
- Less unplanned downtime, thanks to preventative maintenance
- Secure remote access to diagnostics and reporting
- Simpler training, operation and maintenance
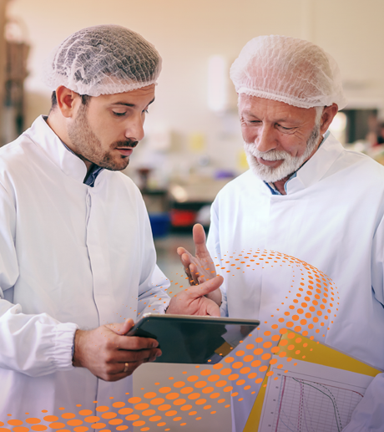
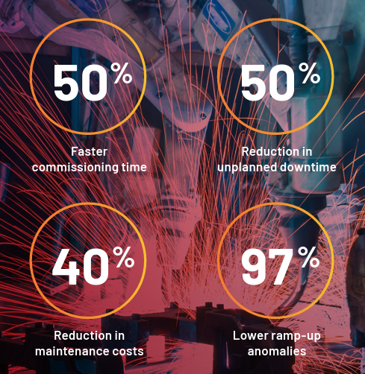
Clear Digital Thinking
Most industrial companies today are investing in digitalization. But the path to digital transformation is a journey – and not necessarily an easy one. Legacy machines often stand in the way of data integration and information transparency. And even newer equipment and systems are often difficult to integrate and cannot deliver the level of production information required to maximize performance.
Most industrial companies today are investing in digitalization. But the path to digital transformation is a journey – and not necessarily an easy one.
Legacy machines often stand in the way of data integration and information transparency. And even newer equipment and systems are often difficult to integrate and cannot deliver the level of production information required to maximize performance.
Success begins with clear digital thinking – not only about how to achieve better customer outcomes and machine differentiation today. But also, about your own digital journey and future goals. And what technologies can get you there faster and cost-effectively.
Smarter machines and equipment deliver differentiated value
Yesterday’s “smart” machines delivered data. But the smart machines and equipment you build today must translate data into insights that drive better decision-making for your customers. Your machines must also provide robust security - and greater connectivity to plant and supply chain networks than ever before. To differentiate, your offerings need a higher level of intelligence. True smart machines and intelligent equipment use digital technologies to move beyond conventional control, operation and maintenance paradigms.
How? Smart devices are the foundation for smart systems – and smarter machines
“Smart” devices connect to a network directly or by using an enabling technology. Smart devices are self-aware and system-aware assets that acquire and process data – and monitor and report on asset conditions such as energy usage and self-diagnostics. Connected smart devices share key system features and collaborate using common software tools and interfaces to improve performance. With the right smart devices, your equipment can deliver information and insights that support a more proactive approach to equipment performance and maintenance – and maximize ROI.
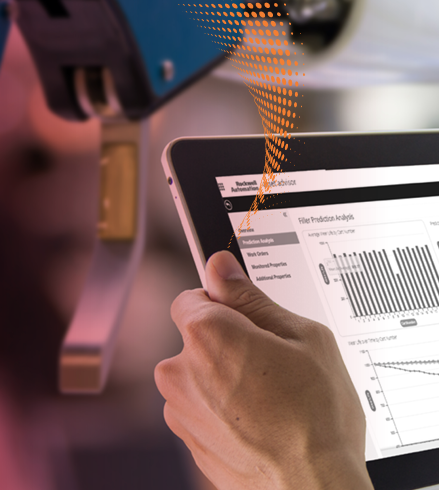
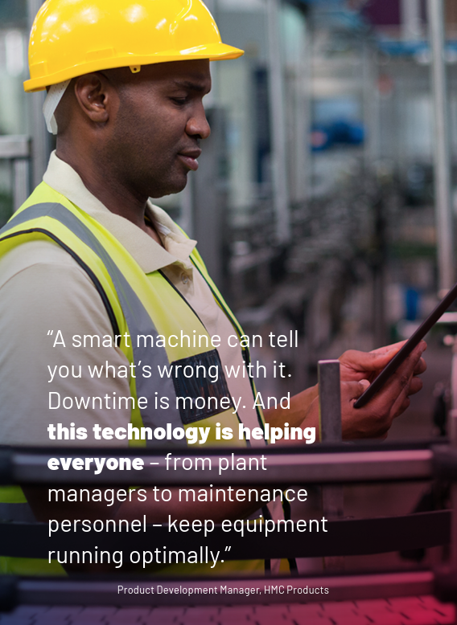
Smarter machines and equipment capture the power of smart devices to do more
- Use self-diagnostics to provide contextualized information regarding asset health, simplify predictive maintenance and minimize unplanned downtime.
- Enable quick visibility to all machine events – including safety events – on the same network platform.
- Use built-in safety features and advanced safety techniques to enhance both safety and productivity.
- Improve response time and asset performance with data – and technologies including adaptive control that make automatic adjustments to maintain desired performance.
With the right smart devices, you can build equipment that meets your customers’ objectives faster.
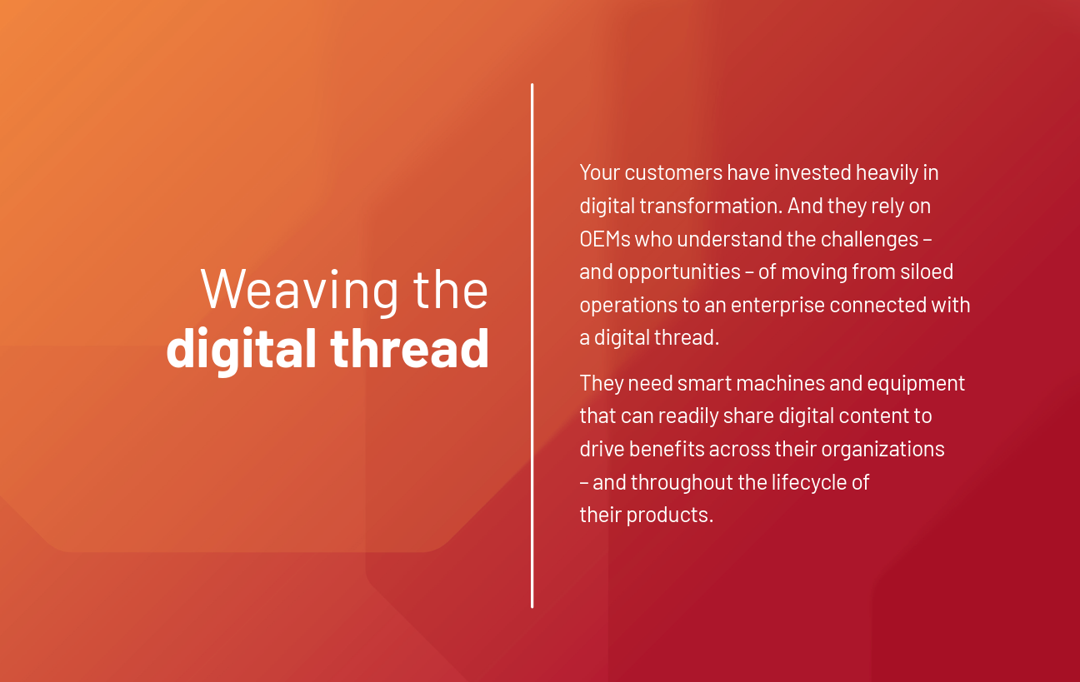
How you can exceed digital expectations
With new transformative technology, your smart machines can share content earlier and more often – and then stay connected to applications across the enterprise and beyond to deliver continuous value.
- Use collaborative design software to partner with manufacturers from the start on equipment designs and incorporate revisions quickly.
- Emulate machine operation – and bring your machines to life with dynamic digital twin software to test “what if” scenarios without risk.
- Validate designs and commission your assets virtually to speed work on-site.
- Provide expert support remotely in real-time – and reduce delays, on-site visits and expense.
- Achieve tighter integration between the supply chain, e-commerce portals and MES systems to help enable a faster manufacturing response better aligned to demand.
It’s all about connectivity – and capturing the power of the virtual world. Your intelligent equipment can do both – and support both your customers’ digital journey and your own.
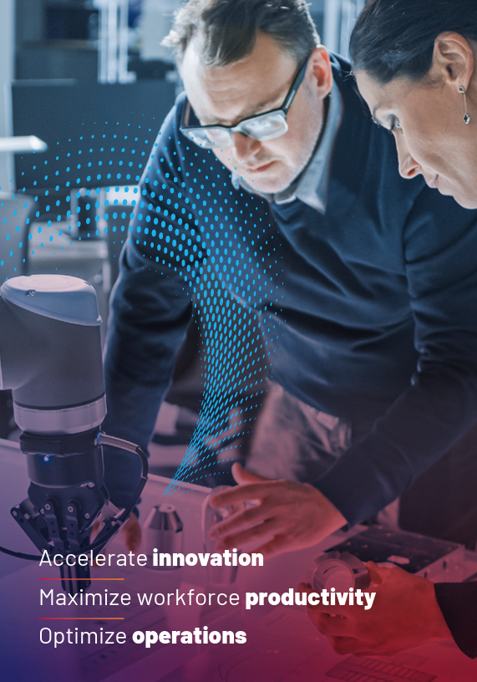
Better productivity, safety & security in a connected environment
No doubt, machine safety or process safety are central considerations in your equipment design. While safety technology and standards will always be critical, connected production facilities require a strategy that goes beyond conventional tools.
Not so long ago, “productivity,” “safety” and “security” were at odds on manufacturing floors. However, in modern connected plants, they are indelibly linked. A security breach on an industrial control system can delay production, damage equipment, injure workers or harm the environment.
How does this impact you?
Manufacturers need smart machines that can bolster productivity – and help manage the safety and security risk inherent to connected operations.
To meet new demands, it’s time to rethink your approach — and consider safety and security in relationship to each other.
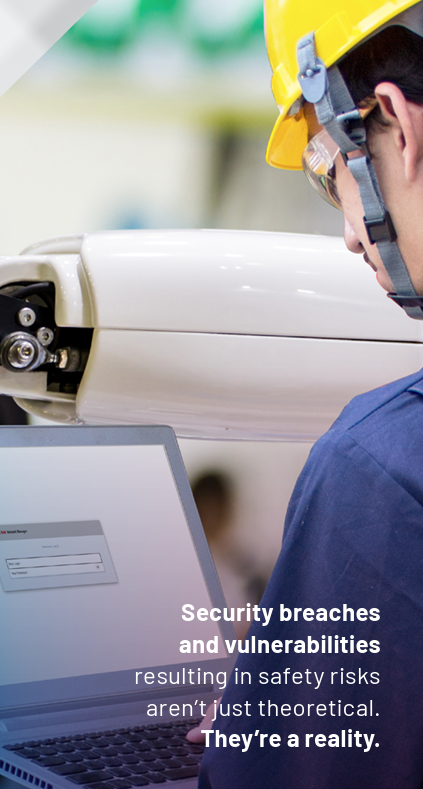
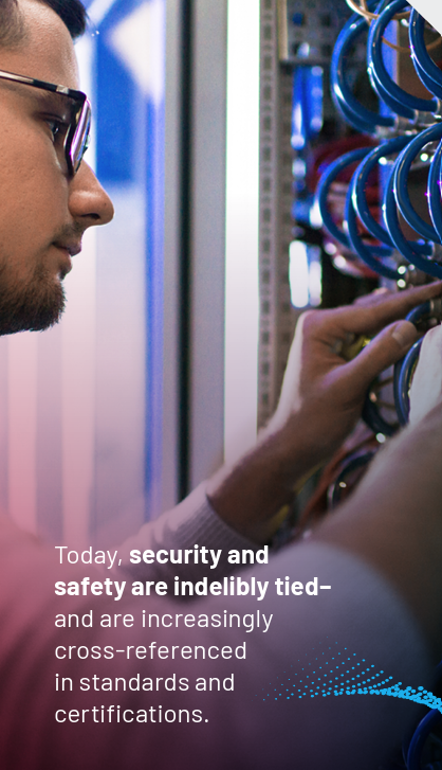
Supporting a Defense-in-Depth approach to cybersecurity
Following global best practices, manufacturers increasingly base cybersecurity on defense-in-depth. This approach uses multiple layers of physical, electronic and procedural safeguards to mitigate risk – and every layer helps.
Your machines are a critical part of this strategy.
Basing your equipment on integrated safety and control products that support the CIP Security™ protocol is one way you can support defense-in-depth. This open standard enables CIP-connected devices to protect themselves from malicious communication in three critical ways:
- Reject data that has been altered.
- Reject messages sent by untrusted people or devices.
- Reject messages that request actions that are not allowed.
A machine properly designed for security and safety protects people and equipment. It also minimizes security-related production interruptions – and improves information collection, analysis and delivery.
You can achieve your goals faster when you choose an automation supplier who can help you assess your risk - and design a solution.
Open new paths to more flexible machines
Optimizing machine performance is your number one priority. But if you’re like many machine builders, you’ve discovered that incremental improvements to equipment based on conventional technology are no longer enough to achieve the flexibility customers demand.
Machines built with static mechanical parts, friction-based conveyance and a plethora of ancillary equipment may achieve high throughput running uniform product with fixed variables. But they are often unable to reach productivity objectives in a “high mix, low volume” world – no matter how much designs are tweaked.
Mechatronics technology removes barriers to flexibility so you can take a clean-slate approach to machine design.
Mechatronics collapses electrical, mechanical and computer technologies into one process. The result? You can achieve unified machine designs that are simpler and more agile.
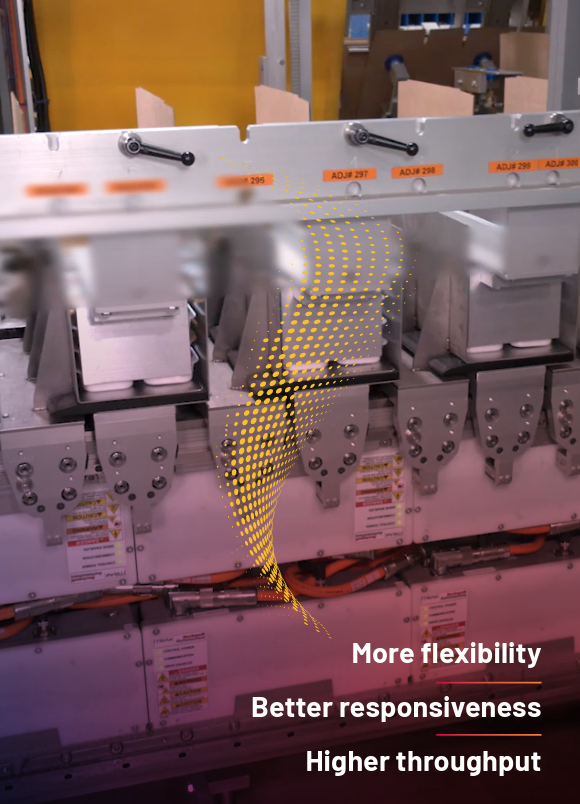
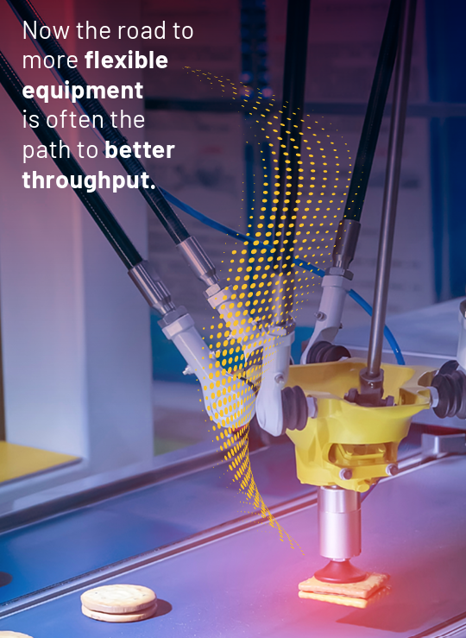
Truly Transformative
With the latest advances, you can combine intelligent mechatronics technologies in a myriad of ways to replace virtually any conventional design. These technologies are transforming assembly, packaging and other applications.
Robotics
Intrinsically flexible, robots operate fully in three dimensions and determine appropriate paths without mechanical rerouting. Robots can address infinitely variable product shapes and process requirements with extraordinary consistency and speed.
Independent cart technology
Conventional conveyors advance product on a preconfigured path at a fixed speed. Independent cart technology boosts machine response to a diverse product mix by moving products intelligently as operations are completed.
Automated changeover
With smart servo motors and drives on changeover mechanisms, machine setup for a new product configuration is achieved with the push of a button.
Because mechatronics replace complex mechanical designs, your machines can do more – with fewer components in much less space. And with emulation and digital twin technology, you can test and confirm your designs in the virtual world to help speed innovation with less risk.
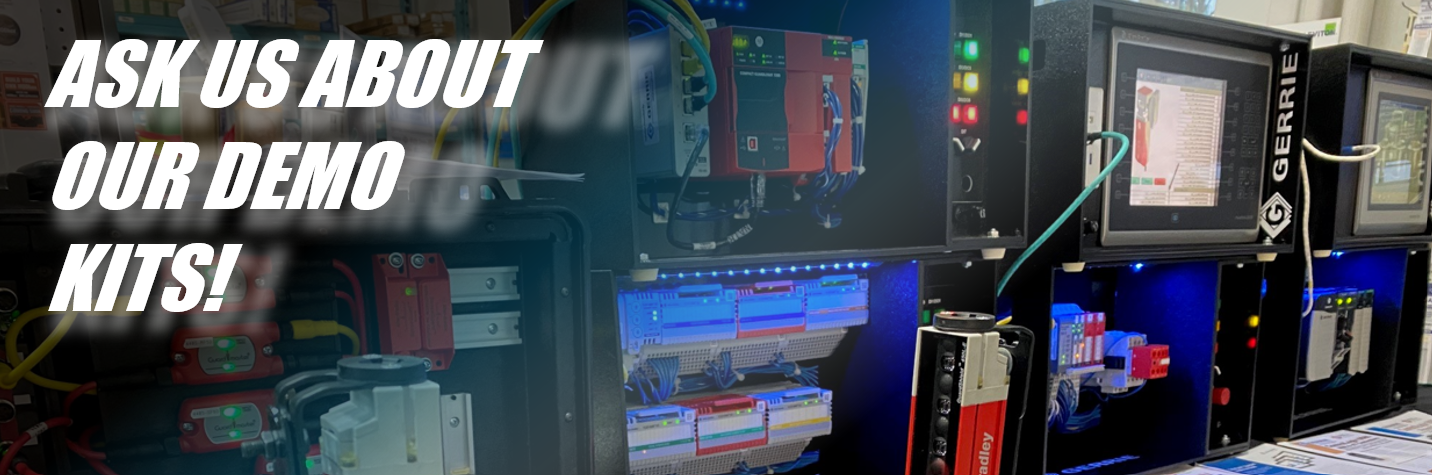
Simple is Better
For every machine you build, you must decide which technologies are most appropriate for the application. And how best to integrate those technologies into the machine and plant architecture.
Advanced technologies from third-party suppliers once came equipped with proprietary control systems. Machine coordination relied on the challenging integration of multiple disparate systems, which added complexity at every stage of your machine lifecycle.
Today there’s a simpler, better way.
Enhanced processor speeds and performance in the latest programmable controllers means you can run advanced technologies like robotics, independent cart technology and automated changeover systems on the same controller that runs the rest of the machine.
Of course, enhanced processing power also equates to faster response times – and that often translates to better productivity and overall machine performance.
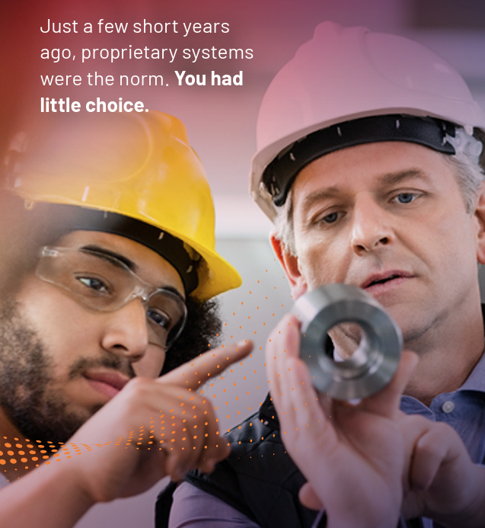
ONE controller
ONE design environment
Unified machine control eases design and integration – and helps you improve your time to market. It also simplifies machine operation and maintenance for your customers, who must only understand and support one system.
But a unified control platform does more:
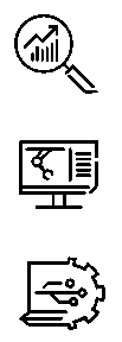
- Provides one unified source for machine data, so you can more easily deliver information in a meaningful way.
- Serves as an ideal foundation for visualization, reporting and analytics solutions.
- Enables better monitoring of the key machine factors affecting performance, efficiency and quality.
Put simply, with unified machine control, you can create smarter equipment that more easily integrates into a facility – and delivers more impactful information and insights.
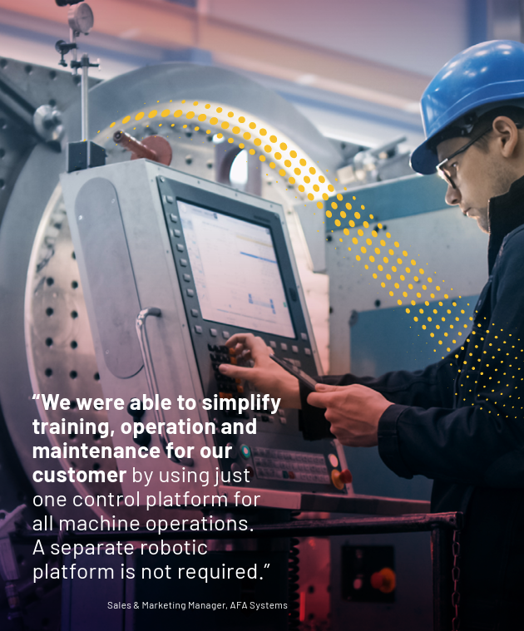
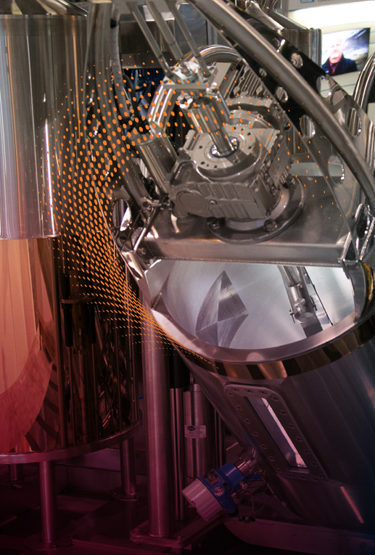
Put your process skid’s intelligence to work
From food and beverage production to biomanufacturing, today’s process industries require agile equipment to keep pace with consumer demand.
If you’re an OEM who delivers modular process skids, enabling fast, efficient changeover is just part of your challenge. You must also design equipment that integrates easily into the plant control architecture – and delivers critical production information to maximize agility.
Your equipment is smarter than ever. But your customers may not be using its native intelligence to the fullest advantage.
After all, customers often view skids as islands of automation. They might specify a piece of equipment to perform an intended action without a bigger vision for the integration of the skid and its information into the rest of the process. Integrating skids across a facility can provide interoperability and access to data, unleashing the power of a Connected Enterprise.
How can you simplify equipment integration and improve access to information?
While you cannot change customer specifications, you can make integration capabilities – and control system scalability – a priority in equipment development.
Step up to a modern DCS
It’s time to take a closer look at the tried-and-true equipment you originally designed for standalone installations. For standard offerings, assume any skid built will be integrated with other equipment.
What if you could ship your skids assembled, tested and ready for integration? How much onsite engineering time would you save?
Basing your process skid control on a modern distributed control system (DCS) can help you achieve your goals.
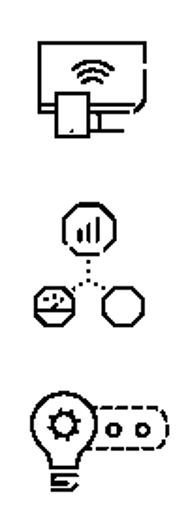
- Improve access to information and simplify integration with skids built on open, unmodified Ethernet and that communicate directly with a wide range of controllers and I/O.
- Use off-the-shelf components to help enable compliance with demanding industry regulations for both batch and continuous applications.
- Add controller-based batch and sequencing to replace engineering intensive custom-coded sequence management – and speed skid delivery, startup and debugging.
Easily scale to meet new expectations
A scalable automation platform improves the flexibility of your offerings and delivers a “win” for both you and your customers.
A truly scalable offering provides options throughout every aspect of the platform – from controllers and I/O through the HMI, batch process control and analytics.
As operations expand, you can apply differentiating information-enabled technology over time.
Thanks to open communication protocols, your customers can capture the value of smarter equipment without a major upfront investment in automation infrastructure – and scale as they grow.
When your offerings expand, take advantage of reusable, plug-and-play enabled tools to streamline your design process. And easily leverage applications and analytics developed from one system to another.
Building your information-enabled future
On every manufacturing floor there is more technology and data available to help solve operational issues than ever before. But connecting data – and transforming it into useful information – remains a struggle. Your smart machines and equipment are a critical part of meeting this challenge and provide the foundation for information-enabled, smart operations.
One way to improve your customers’ opportunity for success? Design your machines for information availability.
And that means standardizing on a control platform and network infrastructure that simplifies integration – and seamlessly and securely connects to analytics platforms and business systems.
How connected machines take information to the next level
Your machines and equipment likely provide descriptive alarming to help improve maintenance and uptime. An alarm that indicates a motor overload has tripped helps with troubleshooting. But a worker still must make multiple decisions about how to react in the moment.
With network connectivity to a robust historical machine database, analytics tools can create models that predict future behavior based on past performance. And use machine learning to optimize operations.
This can be as simple as predicting an anomaly to give an operator time to take preventative steps. Or as sophisticated as enabling your machine to take prescriptive action autonomously – like slowing motor speed – to maintain thresholds and keep equipment running.
MAKING IT INTUITIVE – AND MOBILE
Whether your smart machine is reporting operating conditions or delivering critical alarms, an intuitive visualization platform is essential. The easier your system is to use, the better.
A modern HMI features easy-to-understand, graphic-based displays similar to those workers use on their personal devices. Modern systems also provide faster, more convenient access to information by extending displays to new technologies like mobile devices, thin clients or mixed-reality headsets.
Working smarter
Your customers face an unprecedented skills gap that threatens their ability to operate and maintain equipment. As retirements accelerate and fewer people are available to take their place, manufacturers need a more flexible workforce – and new ways to work smarter.
How can your smart machines step-up to workforce challenges?
Now digital tools take advantage of your machine’s intelligence and network connectivity to simplify training, support and maintenance – and drive higher levels of performance with limited staff on-site.
- Use secure remote access to monitor machine performance – and respond to your customer’s critical situations quickly and from a distance.
- Troubleshoot and support equipment without a site visit through a collaborative remote assistance tool that applies digital twins and augmented reality to share real-time guidance and instructions.
- Transfer knowledge more effectively with a tool that captures step-by-step instructions for machine or equipment procedures as your expert performs them. And then allows less experienced operators to view the recordings in a virtual environment as they perform the same tasks.
- Make your machines “thin client ready” to improve secure remote access to machine applications by the right worker via mobile devices, including cell phones and tablets.
Through virtual environments and digital tools, you can deliver powerful support and differentiated value that helps your customers adjust to new work paradigms.
And the good news is more manufacturers are granting OEMs secure remote access to their equipment.
The result? You can achieve higher levels of customer satisfaction by capturing the power of remote and virtual tools. And build a foundation for a digital service business model – and new revenue streams for your company.
It's time to reimage what's possible.
The right automation partner can help yo transform your "what if" scenarios into reality. Learn more about how powerful digital technologies from Rockwell Automation can make your machines more intelligent, more productive and more connected.
Contact Gerrie Rockwell Automation